Thermocouples are one of the simplest methods of measuring temperature.
Thermocouples do not require a power source to the sensor and, if you select the right one for your application, they are robust and accurate. So, what are the common problems? Read on to find out and discover how to prevent them.
Common Problems with Thermocouples and How to Avoid Them
By Stephen Holt, Technical Manager since 1996
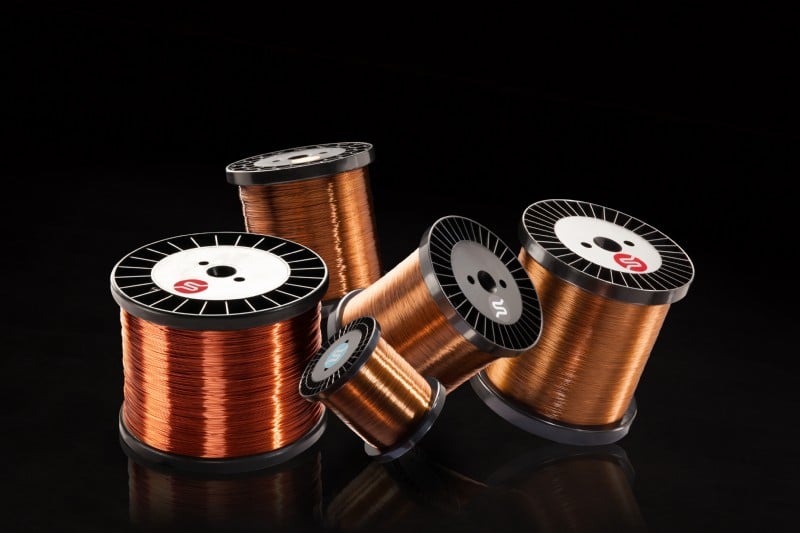
Corrosion
Type K and Type N are made from high Nickel content alloys and are therefore good at resisting corrosion on air. But ‘reducing’ or low oxygen atmospheres can cause the Chromium to preferentially oxidise, altering the chemical composition of the alloy and changing its emf output. Add carbonaceous or sulphur bearing gases and the corrosion effect multiplies causing intergranular expansion and cracking of the alloy.
Type J has a pure Iron positive leg which is particularly susceptible to corrosion in damp atmospheres and finally the Copper in the Type T positive leg will oxidise if taken above 250°C in air.
Protection against corrosion can be achieved by placing the thermocouple conductors in a metal sheath, but all the junctions and extension cabling also need protection to prevent the ingress of corrosive agents.
Ageing
Type K thermocouples experience a particular EMF change if cycled between ambient temperature and 400°C called ‘Ageing’. A rearrangement of the atoms or electrons (nobody has managed to fully explain it yet) causes the emf output to increase, affecting the accuracy of the thermocouple by up to 8°C. This shift can be corrected by taking the conductors up to 700°C but it will remain if the wires are only used below 400°C.
In the 1960s a series of experiments were conducted to find an alloy composition which did not suffer from this shift and it was found that adding Silicon suppressed the emf change. However, the Seebeck coefficients of the new alloys were different from Type K and hence Type N was born. Type N has better corrosion resistance and no ageing problems but a different temperature-EMF profile which means that a new calibration range has to be added to thermocouple meters and this delayed its widespread adoption for many years.
Accuracy
Type K, Type N, Type T, Type R, Type S, Type B, Type E all have different accuracy classes and temperature ranges which are also different depending on which national or international standard they are certified to. Always confirm with your thermocouple supplier the thermocouple type, the temperature range, the thermocouple class and the standard you require.
Polarity and Colour Scheme Identification
As thermocouples became standardised over the 20th century, countries and international bodies developed their own identifying colour schemes for the positive and negative legs and the cable oversheaths for the various thermocouples and compensating leads. This can lead to confusion not only as to which way around they need to be connected but even which thermocouple type you have. Inserting the wrong extension cable in the circuit or incorrectly connecting the polarity will give you some weird and wonderful temperature readings.
Colour charts are available to help identify the various options and even the use of a magnet can assist you as, in some cases, one leg is magnetic and the other is not.
Ground Loops
Some thermocouple probes are ‘grounded’ by being attached to the inside of the protective metal sheath which improves their speed of response. This metal sheath must be grounded in only one place so that currents cannot flow into the thermocouple creating an additional voltage effect. Even fully insulated thermocouples can have voltages induced into them if the protective metal sheathing conducts ground loop currents due to multiple grounding points.
Induced EMF
The EMF output of a thermocouple is relatively small. This means EMF interference can create significant inaccuracies in the reading. Ensuring the thermocouple and it’s cabling is effectively shielded or that the thermocouple extension cable is run in a separate conduit to active power cables will mitigate induced EMF problems.
The Type E thermocouple pair has the highest voltage output profile and using this Nickel/Chrome vs Copper/Nickel alloy combination can also help to reduce the impact of any EMF interference.
Old Age
Thermocouples are high temperature devices and regular exposure to high temperatures, repeated temperature cycling and even physical abuse will have a detrimental effect on the metallurgy of the thermocouple elements causing irreversible changes. These usually act to reduce the EMF output from the sensor until it is no longer within the required accuracy. If the thermocouple is being used in a critical situation it should be regularly calibrated so that a decision can be taken when to replace it.
Cold Junction Compensation
At the ‘cold end’ the thermocouple circuit the alloy wires have to be connected to copper leads to feed into the meter. It is necessary to know the temperature of this junction as the thermocouple emf output is proportional to the differential temperature between the probe tip and the cold junction. Cold junction compensation is the term used for the process of measuring the temperature of the junction between the thermocouple alloys and the copper meter leads, which may actually take place within the meter itself, and adjusting the ‘measured’ voltage to take account of this. If the cold junction compensating sensor becomes faulty the ‘zero point’ of the thermocouple circuit becomes uncertain, affecting the indicated temperature reading.
Failure of the CJC process can be difficult to diagnose as it may not create an obvious ambient temperature offset. A full calibration process of each part will confirm if this is the issue.
Consistency of the Thermocouple Wire
The emf in a thermocouple is not only generated at the two junctions (the Peltier effect) but also by the temperature gradient along the whole length of the thermocouple conductors (the Thomson effect). This means the composition of the wires must be consistent along their whole length as severe temperature gradients may be found well away from the probe tip, such as where the sensor runs through the side of a furnace into the ambient environment. Scott Precision thermocouple wires are carefully manufactured to provide this consistency along every meter of conductor.
If you would like to discuss your requirements with one of the expert team at Scott Precision please contact us by email, contact form or phone.